Forklift safety is a key topic in any type of manufacturing and distribution facility. Forklifts are one of the most dangerous pieces of equipment that facilities like this have. If not used properly and with heavy precaution they can cause serious damage, injury and even death.
The following are 28 key points to using, managing and maintaining forklifts. These items should be reviewed by managers and employees on a regular basis.
1. KNOW YOUR RESPONSIBILITIES
Maintaining and improving forklift safety is up to the efforts of multiple different parties. And each has its own responsibilities. Let’s briefly go through them:
Employers, Supervisors, and Managers
These individuals should:
- Create a comprehensive written forklift safety training program.
- Ensure all operators receive proper forklift safety training.
- Place only experienced and competent staff in supervisory roles.
- Monitor employees for compliance with safety rules and protocols.
- Make employees aware of potential hazards.
- Continually identify ways to improve safe operations in the workplace.
- Abide by all government regulations and company policies.
Forklift Operators
What are the duties and responsibilities of a forklift operator?
Here are some of the key ones:
- Complying with all government regulations and company policies.
- Wearing proper personal protective equipment (PPE) when working with hazardous substances like fuel and batteries.
- Reporting any equipment defects to supervisors for correction.
- Working safely at all times in ways that don’t endanger themselves, coworkers, or the facility.
2. CONDUCT PROPER OPERATOR TRAINING
Quality forklift training is the single best way to improve forklift safety. In fact, OSHA estimates that 70% of errors can be prevented by properly trained operators!
So, what goes into “proper forklift training?” Overall, OSHA requires that employers provide:
- Formal instruction: This includes classroom-based lessons that cover all 22 forklift safety topics listed in standards; 1910.178(l)(3)(i) and 1910.178(l)(3)(ii).
- Hands-on training and evaluation: This is where a qualified instructor demonstrates how to operate a forklift and observes students doing so.
- Certification: This is where the operator trainee is observed using the forklift in the actual workplace.
Training doesn’t stop there. OSHA also mandates that employers provide refresher training at least every 3 years. If operators are observed doing something unsafe, or if workplace conditions change, you’ll have to provide refresher training more often.
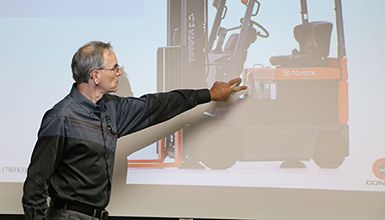
3. INSTALL AND MAINTAIN SAFETY GUARDS
Wondering what safety guards do forklifts have? The answer is that the main ones are the overhead guard and load backrest. OSHA requires that forklifts have an overhead guard installed.
These protect the operator from falling objects. You should regularly inspect your overhead guards for defects like unauthorized holes and dents. When found, the truck should be placed out of service until the guard is replaced. A load backrest is also required by OSHA when there’s a hazard of the load falling backward.
This safety guard helps to keep the load in place. But often, operators will remove the load backrest. The reason is usually so they can access higher levels without hitting the ceiling. But this can increase the chances of items falling off the load. So whenever possible, keep the load backrest installed for added security.
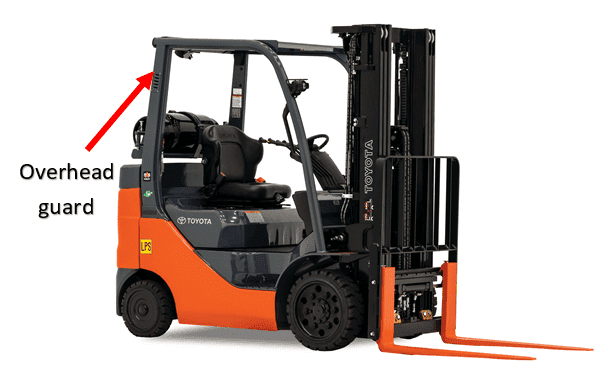
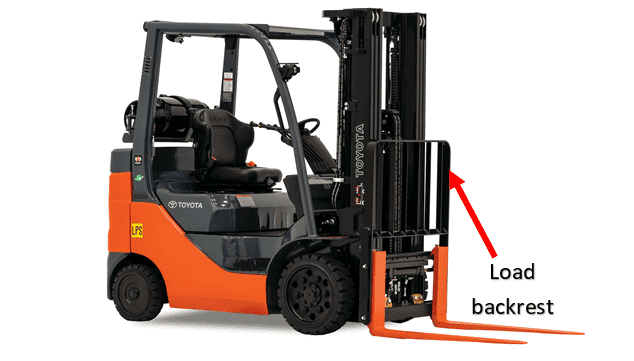
4. DO NOT MODIFY YOUR FORK TRUCK
If you’re thinking of making modifications to your forklift yourself – STOP and discuss why with your manager! Modifications will violate OSHA’s rules, which state:
Modifications and additions which affect capacity and safe operation shall not be performed by the customer or user without manufacturers prior written approval. Capacity, operation, and maintenance instruction plates, tags, or decals shall be changed accordingly. OSHA Standard 1910.178(a)(4).
One particularly worrisome modification that we sometimes see is drill holes in the overhead guard. This is usually done to mount accessories like mirrors and safety lights. But even small drill holes can affect the integrity of the overhead guard. And that is a major safety concern.
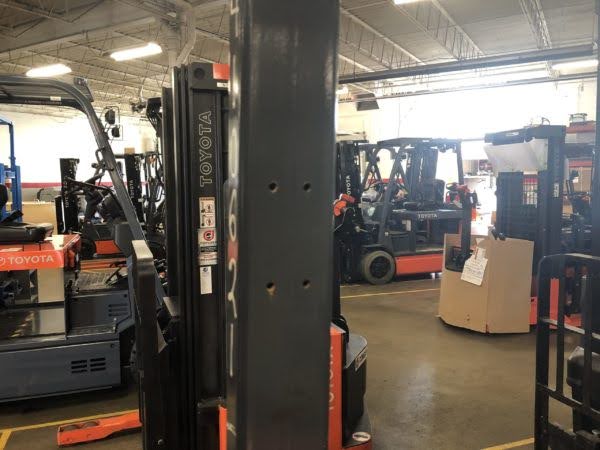
5. USE PROPER LIGHTING
Forklifts are commonly used in low-light areas, like warehouses, semi-trailers, and rail cars.
When operating in these areas without proper lighting, operators are more likely to ram into pedestrians or products.
It’s important to have fork truck safety lights to minimize this. How much light is too little light? OSHA says the limit is anything less than 2 lumens per square foot. For reference, an average bedroom is between 10 to 20 lumens per square foot.
6. INSTALL GAS DETECTORS
Liquefied petroleum gas (LPG) powered forklifts are often used indoors. That’s because they emit fewer dangerous gasses like carbon monoxide (CO) than gasoline or diesel engines do. That said, it’s still crucial to monitor the concentration of these gasses in your work environment.
If not, workers nearby can become seriously ill or even die due to carbon monoxide poisoning.
But what exactly is the CO limit? OSHA says that it must not exceed 50 parts per million (ppm) at 77° F and 760 torr. That equates to approximately 55 milligrams per cubic meter of air.
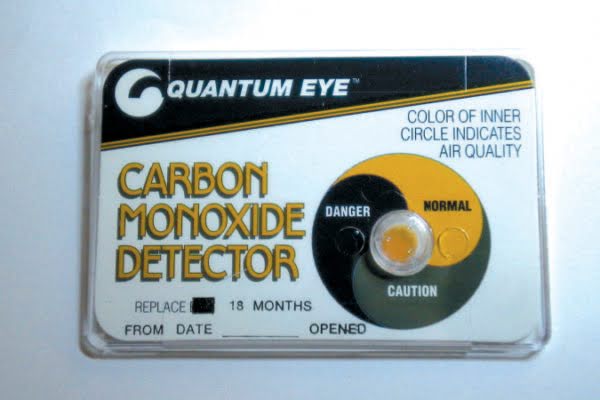
7. USE CARE WHEN LOADING AND UNLOADING TRAILERS
One of the main things forklift operators do is load and unload semi-trailers at the dock. But this routine activity carries plenty of risks if proper procedures aren’t followed.
What are those procedures?
- Ensuring semi-truck brakes are set and the wheels are chocked.
- Using fixed jacks to support a semi-trailer when it’s not coupled to the tractor.
- Properly securing dock plates.
- Ensuring the lift truck plus the load doesn’t exceed the dock plate’s rated capacity.
By following these procedures, operators can help avoid dangerous situations like run-away trailers and falls from the dock.
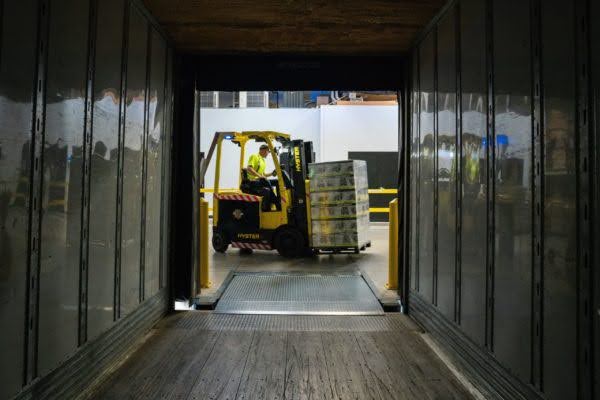
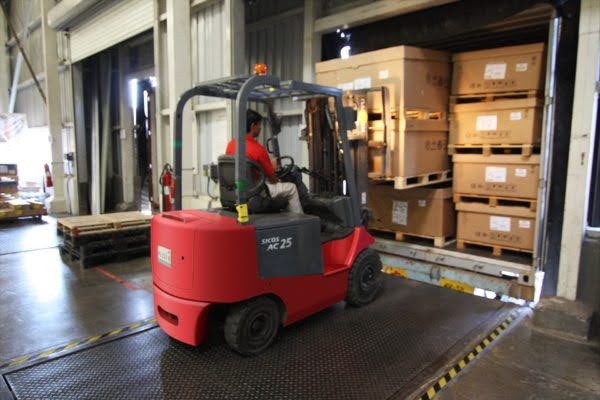
8. INSPECT BEFORE OPERATING
OSHA requires that all forklifts be inspected before being operated. Why should this be done? To determine the safety of the lift truck. These inspections are typically performed by the operator.
Using a checklist, the operator should walk around the fork truck and examine the key areas for any signs of wear, damage, or deficiency. Anything found in poor condition should be noted, reported, and corrected before operating.
9. KEEP UP ON MAINTENANCE
Forklift maintenance is key to ensuring your forklifts last as long as possible. But it’s also a major component of forklift safety procedures. After all, a defective forklift component – like brakes – can result in injury, fatality, and damage to the product.
So, it’s important to keep up on regular maintenance activities. If you have an in-house maintenance team, ensure they follow up on any issues noted by your operators. And if you don’t have an in-house team, consider outsourcing your forklift maintenance to a reliable service center.
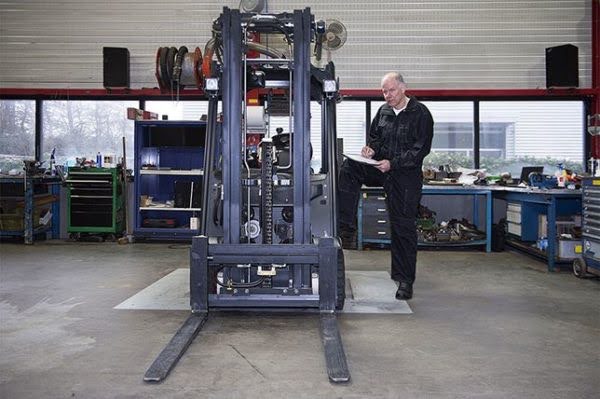
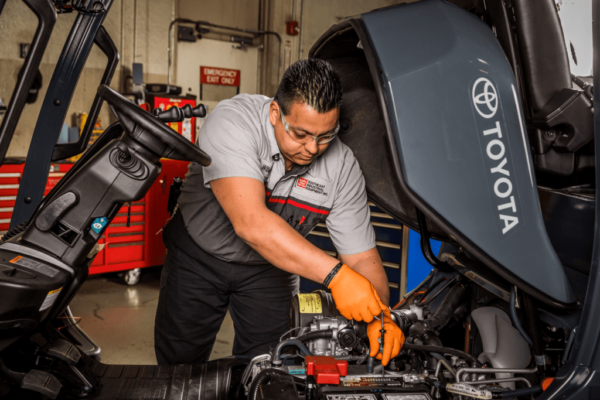
10. KNOW HOW TO SAFELY DISMOUNT A TIPPING LIFT TRUCK
The number one cause of forklift deaths is tip-overs. So knowing how to handle a situation like this is critical.
The guidance for these incidents, however, is different depending on the type of lift truck you’re using. If you’re operating a sit-down style fork truck and it starts to tip, you should:
- Stay in your seat
- Brace yourself
- Lean away from the point of impact
Here are the standup forklift safety tips if you’re operating a stand-up rider forklift that starts to tip:
- Step back from the operator compartment
- Move as far away from the truck as possible
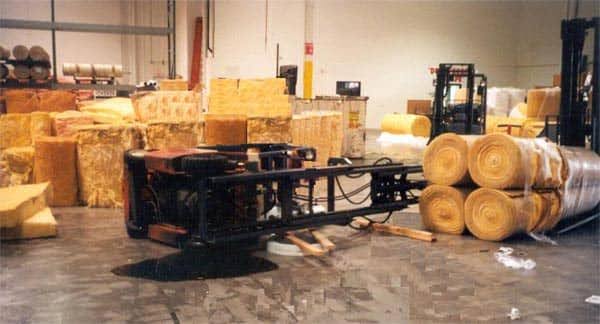
11. INSTALL AN OPERATOR RESTRAINT SYSTEM
What is the most important safety device on a forklift? Answer: The seat belt. Why? Because seat belts are the best way to prevent operators from being crushed in the event of a tip-over.
Sit-down rider forklifts manufactured after 1992 are required to have seat belts installed from the factory. But if your forklifts are older than 1992 models, you should still arrange to have seat belts installed on them. Furthermore, managers should ensure that their maintenance activities include replacing any worn or damaged seat belts.
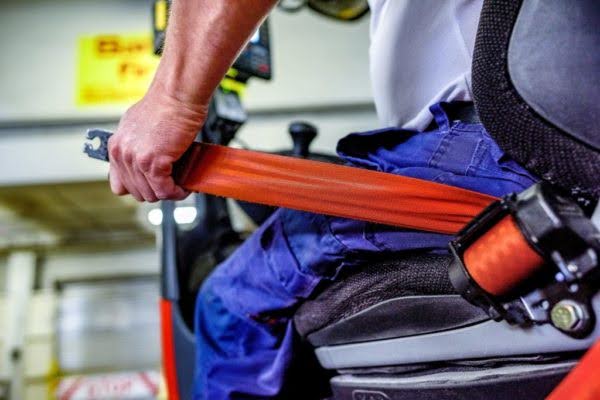
12. DON’T SPEED
Speed kills! And considering that the average warehouse forklift weighs around 9,000 lbs., this adage is especially true. Because with that much weight, forklifts take longer to stop.
How long does it take to stop a forklift at full speed? According to National Safety, Inc. it’s as follows:
- At 4 mph it will take 17 feet to come to a stop
- At 8 mph it will take 42 feet
- And at 9 mph it will take at least 51 feet
Now, you might be wondering: What is the maximum safe speed for a forklift? The University of Rochester recommends:
- 8 mph when no pedestrians are present
- 3 mph when pedestrians are present
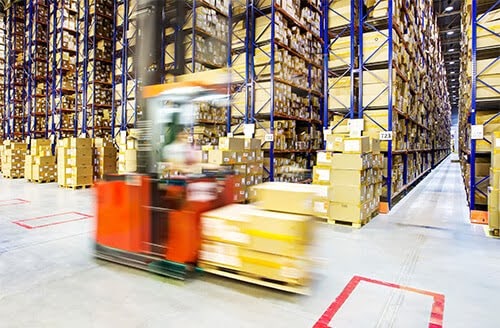
But keeping operators under the speed limit can be a challenge. Fortunately, facility managers who struggle with this have an effective option: Electronic speed control.
Many modern forklifts have this feature standard from the factory. All it takes is having the dealership set the speed and a password to prevent unauthorized changes.
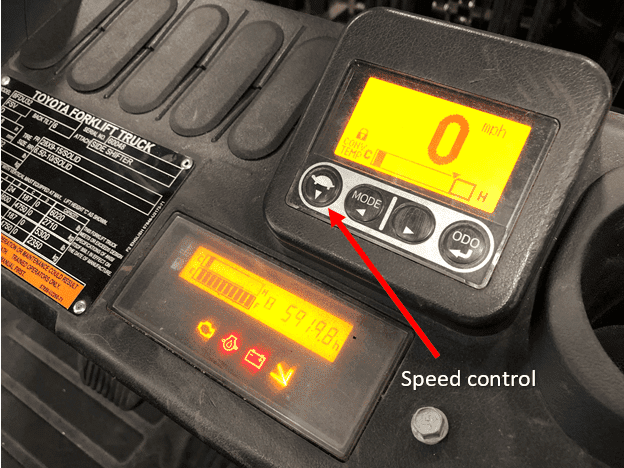
13. HANDLE LOADS PROPERLY
Forklifts are designed to pick stuff up and put them down. But proper load handling isn’t quite that simple. That’s because loads come in all different shapes, sizes, and weights.
So ensuring your loads are stable and balanced is key. To do so, operators should make sure they:
- Use extra caution when handling off-center loads.
- Secure loose items on loads to prevent them from falling.
- Put the forks as far as possible under the load.
- Refrain from tilting unless directly above the deposit position.
Following these load-handling safety tips will help minimize falling loads as well as forklift instability.

14. KEEP A CLEAR LINE OF SIGHT
Forklift operators routinely deal with oversized loads that obscure their vision. But it’s crucial to maintain maximum visibility at all times to prevent accidents.
Thus, operators should take precautions when their sight is blocked. This includes:
- Traveling backward when the load blocks their view.
- Slowing down and honking the horn at intersections.
- Using a forklift spotter to navigate blind spots.
Facility managers can help in this effort by installing mirrors on lift trucks and at intersections.
A common question is: Does OSHA require forklift mirrors? According to EHS Daily Advisor, OSHA doesn’t specifically require them. But if they’re factory-installed, they must not be removed.
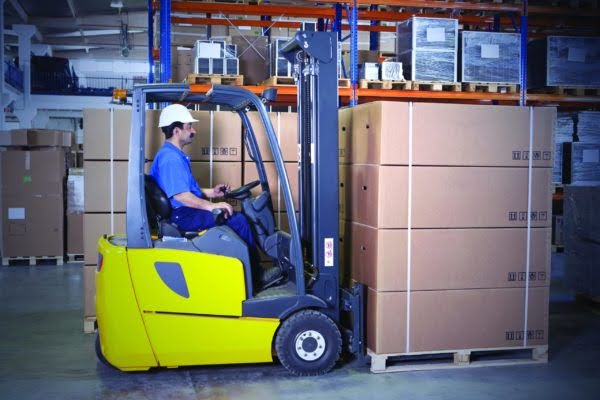
15. LOOK OUT FOR PEDESTRIANS
Of the many things forklift operators have to look out for, pedestrians are the biggest concern. In fact, the U.S. Bureau of Labor Statistics found that pedestrian collisions resulted in 13% of forklift fatalities in 2017.
Operators can improve how they interact with pedestrians in the following ways:
- Sound the horn around corners or any areas where you don’t have a clear view.
- Make eye contact with pedestrians to alert them to your presence.
- Grant pedestrians the right-of-way whenever you encounter them.
- Use verbal or hand signals to let pedestrians know your next move.
- Never drive up to a person who’s in front of a fixed object.
Pedestrian safety isn’t all on the operators, however. By doing the following, pedestrians can help minimize their risk of collision with forklifts:
- Walk on the right side of the aisles.
- Keep distance from operating forklifts.
- Watch out for tail swing to avoid being pinned.
By keeping in mind these forklift pedestrian safety tips, you can greatly improve safety in your workplace.
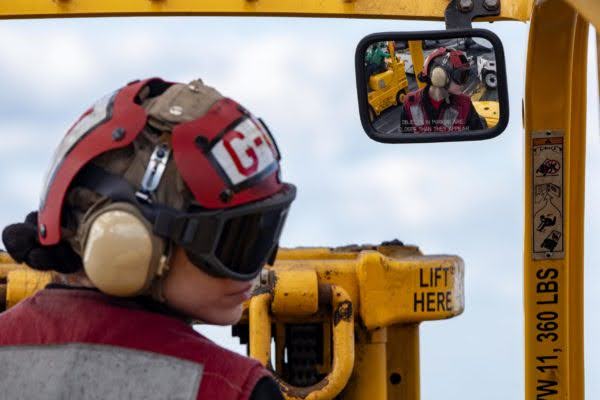
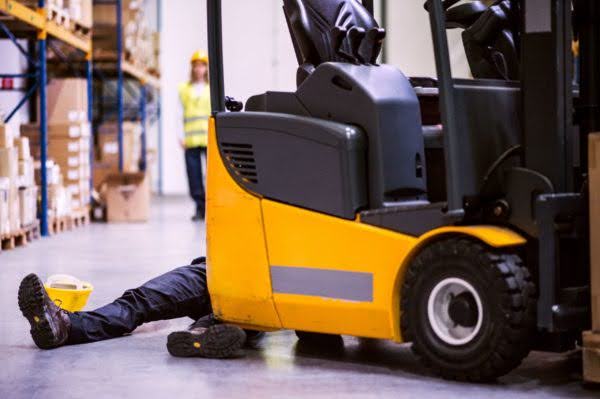
16. SEPARATE FOOT AND FORKLIFT TRAFFIC
Separating the different types of traffic in your facility can go a long way towards improving pedestrian safety. We’ve covered many pedestrian safety tips in the previous section.
But because this is so important, we wanted to include a few more:
- Keep proper aisle widths to allow safe distances between equipment and workers on foot.
- Mark pedestrian and forklift traffic in aisles.
- Keep some aisles designated for pedestrian- or forklift-only traffic.
- Limit the use of forklifts near places where pedestrians congregate. This includes break rooms, restrooms, time clocks, and exits.
- Install physical barriers and pedestrian safety gates around workstations and walkways
- Install forklift traffic signs to alert foot traffic to the presence of equipment.
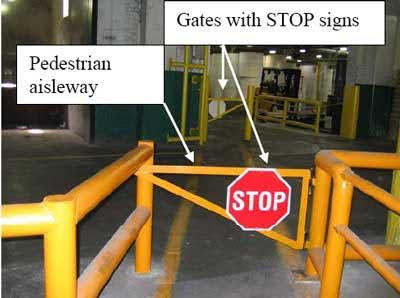
17. DO NOT ALLOW PASSENGERS
Can you carry passengers in your forklift? The answer is no – unless there’s a designated seat for them. Because without a safe spot for passengers, they’re at greater risk of harm if the lift truck tips over.
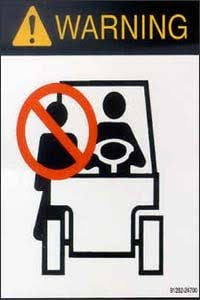
18. USE THE RIGHT EQUIPMENT TO ELEVATE WORKERS
Falls from forklifts caused 15% of forklift fatalities in 2017. How does this happen? Usually, it’s when the forklift operator allows a coworker to stand on the forks while they lift them to the worksite. But this is extremely dangerous. Because even a fall from as little as 7 feet can cause death.
So, what’s the solution? Ideally, you should only lift personnel with equipment designed exclusively for that purpose. And that means using mobile elevated work platforms (MEWPs), like scissor lifts and boom lifts. But if you don’t have this equipment available, there’s another option: Lifting cages.
Personnel can enter the cage, secure themselves, and be safely lifted to their work height. Just make sure that you follow a few rules when working with forklift safety cages:
- Use only approved lifting cages.
- Secure the cage to the carriage or forks.
- Use restraining devices like body harnesses to secure workers to the cage.
- Never drive with the cage elevated.
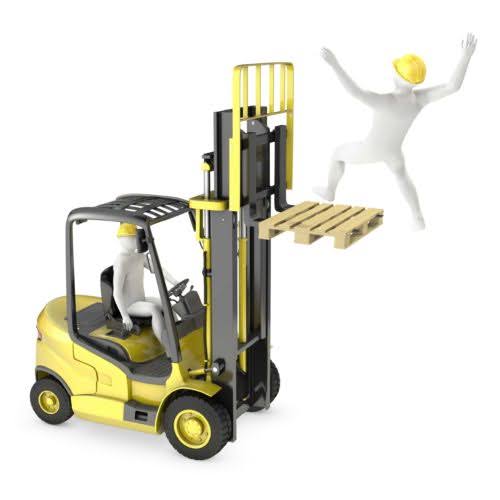
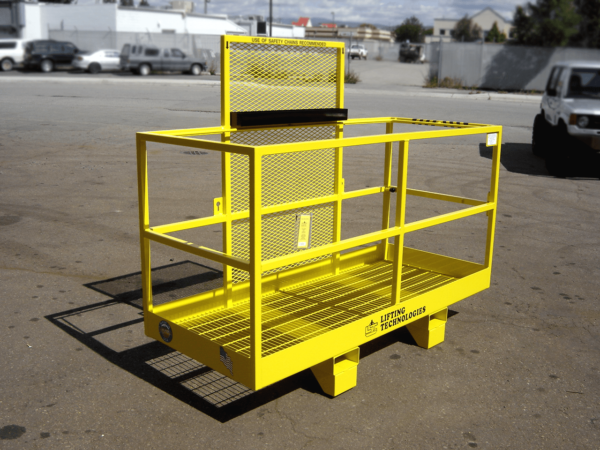
19. ASCEND AND DESCEND RAMPS PROPERLY
Navigating ramps is one of the most dangerous activities for forklift operators. The reason is that even slight grades can cause the forklift to become unstable. This is magnified if the operator turns while on the ramp. Because doing so can easily cause the fork truck to tip over. To minimize the chances of this happening, operators should:
- Drive slowly up and down ramps.
- Drive with the load upgrade to minimize the chances of it falling off the forks.
- Never turn on a ramp if at all possible.
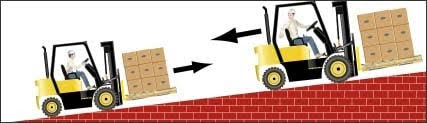
20. SECURE UNATTENDED FORKLIFTS
It’s not uncommon for some lift truck operators to spend their entire shift on their forklift. But more often than not, operators are on and off their lift trucks throughout their day.
If that’s the case, it’s necessary to take proper precautions when leaving a lift truck unattended.
Now, you might be wondering: At what distance is a forklift considered to be unattended? Fortunately, OSHA provides an answer to this question:
A powered industrial truck is unattended when the operator is 25 ft. or more away from the vehicle which remains in his view, or whenever the operator leaves the vehicle and it is not in his view. OSHA Standard 1910.178(m)(5)(ii)
In that case, the operator has a responsibility to secure their lift truck by:
- Lowering the forks completely.
- Turning off the power.
- Setting the parking brake.
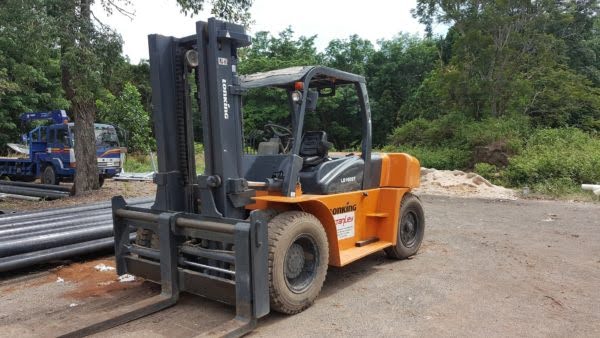
This brings up another popular question: Can you leave keys in a forklift? We couldn’t find where OSHA specifically addresses this. But the answer should be “No.” Why should you remove the key from your forklift? Because it’s simply a best practice to prevent unauthorized people from powering up the lift truck.
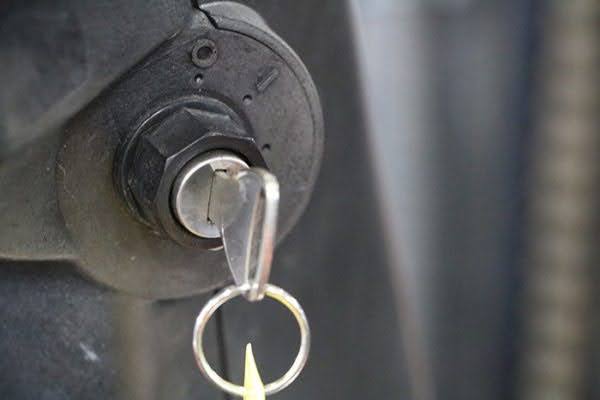
21. KEEP YOUR EQUIPMENT CLEAN
Fork trucks should regularly be cleaned to ensure they operate efficiently. After all, many lift trucks are used in extremely dirty environments.
In those environments, debris and dirt accumulation can interfere with the mechanical components of the truck and limit its performance. Another reason to keep your lift trucks clean is for safety purposes. If the truck has grease and grim on the steering wheel, pedals, or control levers, the operator’s grip won’t be as secure. Without a secure hold, the operator won’t have total control over their lift truck. This can result in serious accidents.
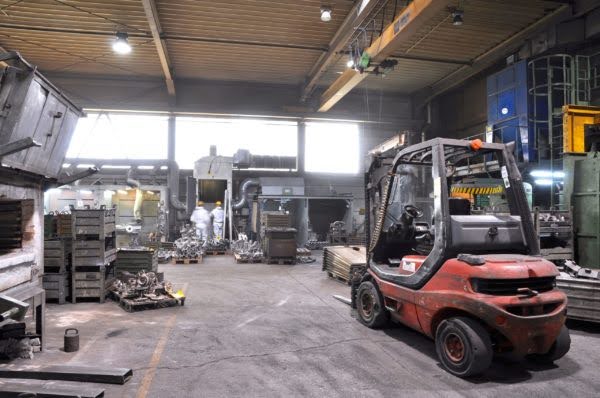
22. FOLLOW SAFE REFUELING PROCEDURES
Most fork trucks run on either LPG, gasoline, diesel, or electricity. And each of these fuel sources poses risks when it comes time to refuel.
Operators should be aware of the safety procedures when refueling and ensure they follow them closely. Some forklift propane safety tips include:
- Turning off the engine on internal combustion (IC) lift trucks before refueling.
- Eliminating ignition sources (like smoking) when near fuel sources.
- Following safe lifting procedures as a full LPG tank can weigh over 84 lbs.
- Wearing proper personal protective equipment like a face mask and gloves when handling propane
Forklift battery safety tips include:
- Charging batteries for electric lift trucks only in designated areas.
- Using proper material handling equipment for removing batteries.
- Not smoking in the charging areas.
- Opening the hood when charging to ventilate and dissipate heat.
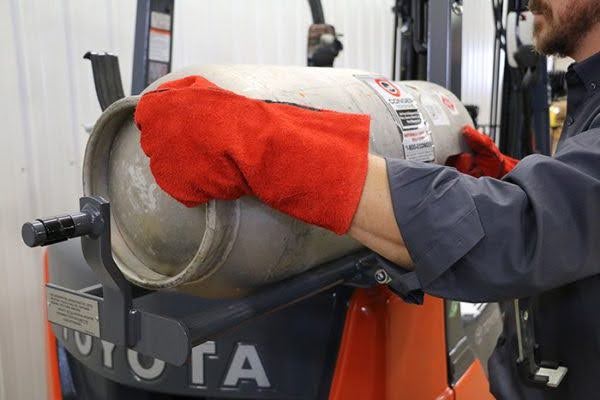
23. NEVER WALK UNDER ELEVATED FORKS
This tip is for pedestrians. Why is it important not to walk under the forks of a lift truck?
- The operator may not see and inadvertently lower the load on the pedestrian.
- An unstable load may fall off the forks and onto the pedestrian.
- The lifting mechanism can malfunction and come down on the pedestrian.
Whichever scenario it is, it’s not a result that anyone wants. If you see an elevated forklift mast, maintain plenty of space and walk around it.
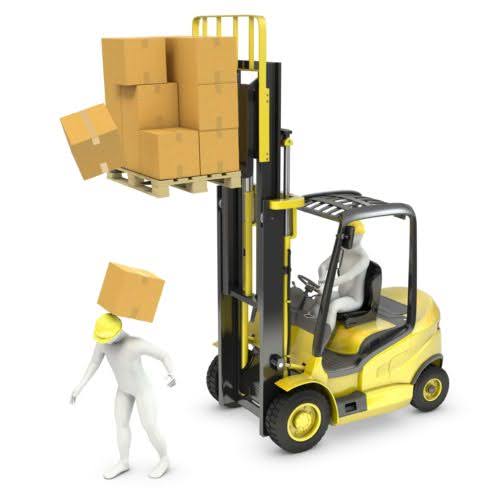
24. KEEP YOUR WORK ENVIRONMENT CLEAN, CLEAR, AND IN GOOD REPAIR
Without a clean and safe work environment, the chances of a forklift accident go up. To reduce this, employers should:
- Conduct regular walk-throughs to identify obstructions and clutter that pose a risk and make plans to correct them.
- Keep stairways and escape routes free of obstructions.
- Inspect and repair any cracks or damage to key areas like loading docks and pallet racking.
Forklift operators can do their part by first walking any routes that may be obstructed. Then, they should clear the obstructions before proceeding.
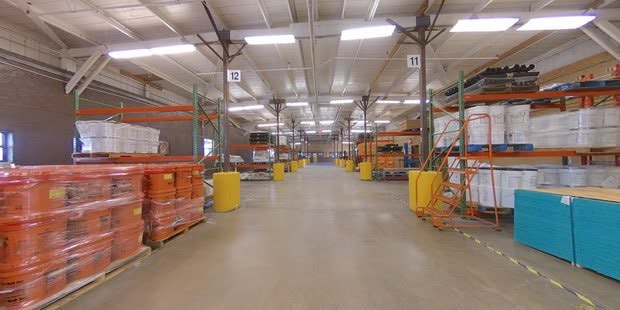
25. DO NOT RUN OVER DEBRIS
If you follow the previous safety tip, you can do a lot to eliminate this hazard. Still, especially tough work environments will never be totally free of debris.
In that case, forklift operators should do everything they can to avoid running it over. Why? Debris can chunk out tires, cause damage to critical forklift components, and introduce instability. When that happens, the risk of a forklift accident goes up. And so does the cost of maintenance and repairs.

26. BE MINDFUL OF THE HAZARDS OF YOUR FORK TRUCK
One of the most dangerous components of a lift truck is the mast. If you’re unfamiliar, this is the mechanism that allows the forks and load to travel up and down. Because of its design, the mast can cause serious injury to anyone who places a body part within it.
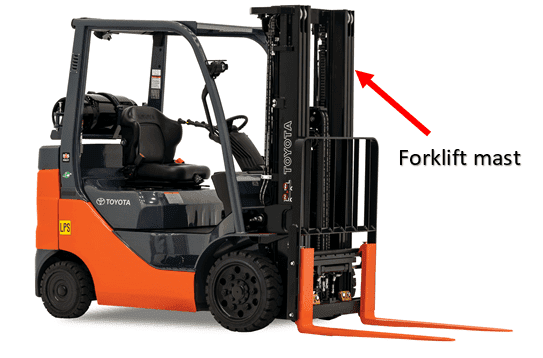
Always keep fingers, hands, and limbs away from the chains, the rails, and the pulleys. Furthermore, operators should never ride with their arms or legs outside the operator compartment. That includes the common practice of putting your hand on the rear overhead guard post when backing.
If an operator does so, they can easily crush their hands against a fixed object like a wall. And that can cause serious injury.
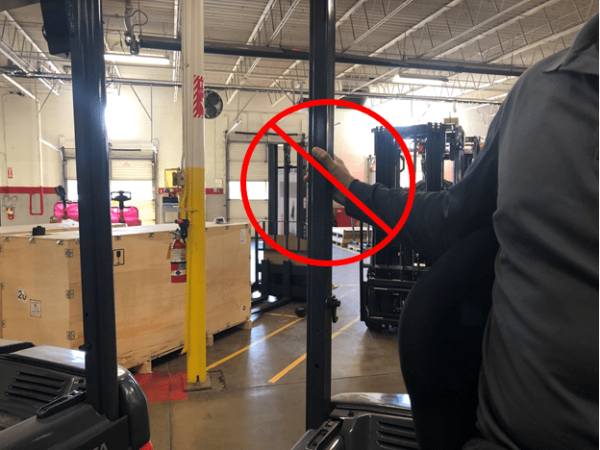
27. NEVER EXCEED THE RATED CAPACITY
Forklift trucks are usually referred to by their nominal capacity. For instance, a 5,000 lbs. forklift is rated to lift 5,000 lbs. at a specified height. This can be misleading, however. That’s because attachments like side shifters can reduce the actual lifting capacity of the lift truck. So, you must understand the true weight lifting ability of your fork truck. How do you do that?
By checking the data plate. It will list any attachments and show exactly how much weight the truck can lift at specified heights. Once you know that information, never lift anything that exceeds that limit. Doing so can cause a whole host of problems, like tip-overs, falling loads, and loss of control.
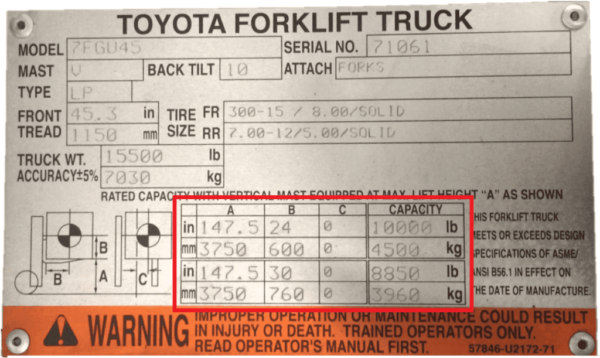
28. DON’T TALK AND OPERATE
Distracted driving isn’t just a problem on the open road. It’s also a huge issue for facilities that operate forklifts. And among the main problems is the use of cell phones.
Operators should never talk or text while operating their forklift. And pedestrians should take extra care when using their phones while in proximity to lift trucks.
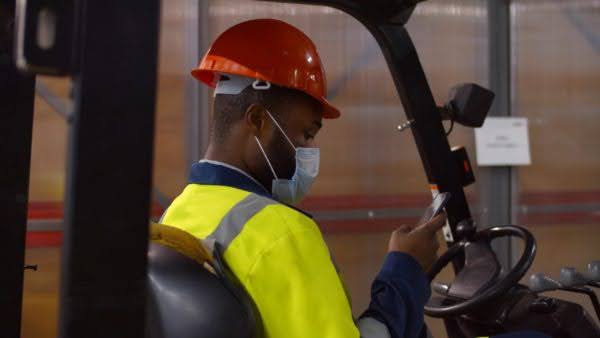
SUMMARY
In summary, forklifts can be the cause of some very serious accidents and issues but with some due diligence and care your work environment can have a very safe and productive facility.